Cancer patient gets world’s first 3D printed ribcage
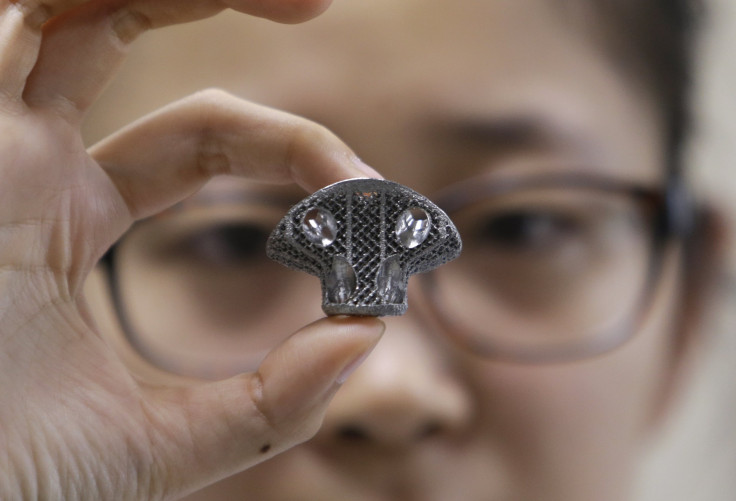
A Spanish cancer patient has received the world’s first 3D printed titanium sternum and rib cage designed and manufactured in Australia. After being diagnosed with chest wall sarcoma, a type of cancerous tumour that grows around the rib cage, the 54-year-old patient was recommended to have his sternum and a portion of his rib cage replaced.
The surgical team, composed of Dr José Aranda, Dr Marcelo Jimene and Dr Gonzalo Varela from the Salamanca University Hospital, determined that a fully customisable 3D printed titanium sternum and rib cage is the best and safest option because this part of the chest is notoriously complicated to recreate with prosthetics. The implant was designed and manufactured by Melbourne-based medical device company, Anatomics, which utilised the CSIRO’s 3D printing facility, Lab 22.
Using high-resolution CT data, the Anatomics team created a 3D reconstruction of the chest wall and tumour, which allowed the surgeons to plan and accurately define resection margins. Experts at Lab 22 then manufactured the implant out of surgical grade titanium alloy, using the company’s $1.3 million Arcam printer. “The printer works by directing an electron beam at a bed of titanium powder in order to melt it. This process is then repeated, building the product up layer-by-layer until you have a complete implant,” said Alex Kingsbury of CSIRO's manufacturing team.
Once the prosthesis was complete, the parts were couriered to Spain and implanted into the patient. The procedure, which has been described in the European Journal of Cardio-Thoracic Surgery, was deemed successful by the doctors since the patient was discharged 12 days after the surgery and has recovered well.
This is not the first time that surgeons have used titanium implants, but replacing large sections of the rib cage is considered a novel procedure due to its tricky nature. “While titanium implants have previously been used in chest surgery, designs have not considered the issues surrounding long term fixation. Flat and plate implants rely on screws for rigid fixation that may come loose over time. This can increase the risk of complications and the possibility of reoperation,” said Anatomics CEO Andrew Batty.
The advantage of 3D printing, according to Batty, is its rapid prototyping which is essential when waiting for life-saving surgery. CSIRO is not new in using 3D printing for biomedical applications. In 2014, the company produced the world’s first 3D printed titanium heel bone which was given to a cancer patient who faced amputation of the leg below the knee.
Contact the writer at feedback@ibtimes.com.au or tell us what you think below.