Space System Company Aims To 3D Print Titanium Fuel Tanks
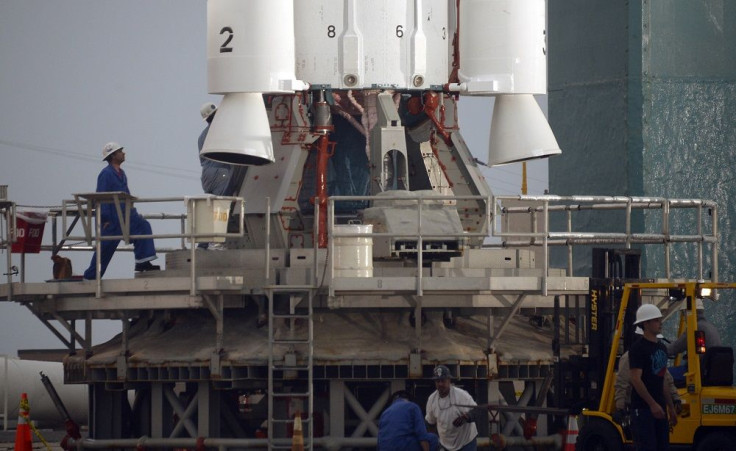
Lockheed Martin Space System, one of the world’s largest defense, aerospace, and advanced technology contractors, is planning to hold the titanium 3D printing of aerospace fuel tanks within their facilities. Lockheed Martin is currently buying fuel tanks made with the Sciaky additive manufacturing process.
The hemispherical halves of these tanks are built layer by layer, with spools of titanium wire being spun for ultimate strength. Now that researchers from Lockheed Martin have studied the process, it has been reported that the company is thinking of moving the construction of these tanks in-house to save money.
The titanium fuel tanks from Orbital ATK were used for the three Mars orbiters. A similar tank will also be used for NASA’s OSIRIS-Rex asteroid probing space vehicle once its construction is completed for the 2016 launch.
The vice president and general manager for Lockheed Martin, Mike Hamel, stated that the company is willing to tweak the adopted technology if the additive manufacturing methods that are being tested will live up to their expectations. Lockheed Martin’s executive vice president for space systems, Rick Ambrose, proposed the company’s use of additive manufacturing techniques. According to 3dprint.com, Ambrose said that it is important to lessen the time constructing satellites, and 3D printing is the key to reach that cut.
In 2014, Lockheed Martin bought a $4 million 3D printing machine from Sciaky Inc. The machine is capable of creating titanium fuel tanks that are 150 centimetres in diameter with half the manufacturing cost of propellent tanks. The additive process is also faster than casting the tanks in molds, which takes about 20 months.
“Manufacturers, for the first time, will be able to utilize Sciaky’s revolutionary additive manufacturing technology to produce production parts and prototypes in their own facility. The possibilities are endless,” stated Sciaky’s general manager, Mike Riesen.
Lockheed Martin is not the only space system company to embrace titanium 3D printing in their products. California-based Space X recently unveiled a manned spaceship with 3D printed rocket engine. Called “Dragon V2,” the spaceship features a propulsion system, superdraco thrusters, and a set of 3D printed titanium engines that produce 32,000 pounds of thrust when activated together.
These advancements in the design and creation of spacecraft are examples of how titanium 3D printing is redefining the aerospace industry. The time will come when more companies will decide to adopt 3D printing for their processes and the bulk demand for titanium will increase too.
Luckily, there will be enough titanium for this technology to thrive in the next coming years with the help of developing mines. Chile’s White Mountain Titanium (OTCQB: WMTM) is on its way to produce 112 million tons of high-grade rutile, securing the world with enough titanium to move forward with additive manufacturing processes.
To contact the writer, email: v.hernandez@ibtimes.com.au