3D Printing Is Breaking Into The Mainstream
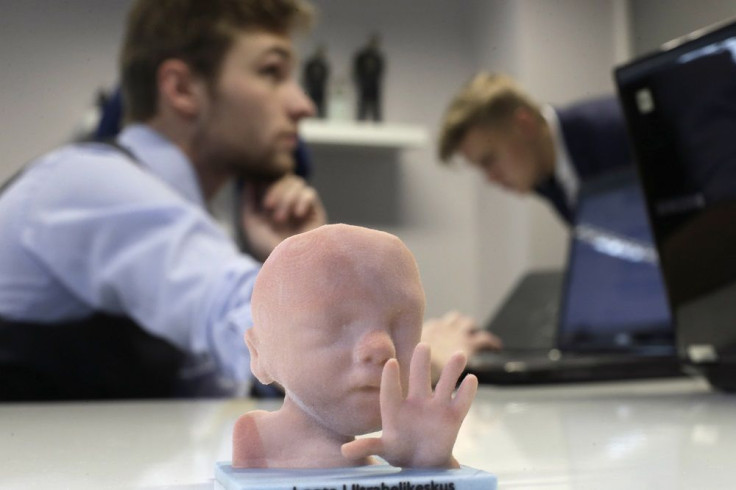
Five years ago, the thought of “mainstream 3d printing” might seem a little far-fetched for the practical manufacturer. However, the technology has advanced in such a rapid pace that the number of industries applying the process continue to increase. At the moment, 3D printing can produce anything from human stem cells to airplane parts. Indeed, the possibilities with additive manufacturing are limitless.
Analysts at research company Gartner said that a technology has officially become mainstream when it reaches an adoption level of 20 percent. In 2014, a PWC survey revealed that more than two-thirds of 100 manufacturing companies were using 3D printing, with 28.9 percent stating that they were still experimenting on processes in which they would implement the in-demand technology.
Additionally, 9.6 percent of the companies revealed that they were in the stages of prototyping and production, and these companies include General Electric, Boeing and Google. Companies that belong to this tier testified to the advantageous effects of 3D printing, which include time saving and cost efficiency. Another survey held by the International Data Corporation, or IDC, revealed that 90 percent of the companies that use 3D printing are very satisfied with its benefits.
Large companies represent biggest buyers of 3D printer, but the high number of smaller and independent businesses opting to use 3D printing is still difficult to ignore. Keith Kmetz, vice president of Hardcopy Peripherals Solutions and Services at IDC, stated that companies that apply 3D printing are well aware of its positive benefits.
“These printers are typically acquired for a specific creation workflow, but once in place, the usage expands rapidly to other types of applications. The early adopters who recognized the substantial cost and time-to-market benefits of 3D printing have carried the day, but it’s their overall satisfaction and the ability to expand usage that will ultimately drive 3D printing to the next level,” said Kmetz.
In the next couple of years, more companies are expected to switch to 3D printing, and more materials will be used for a wide array of products. Currently, the most commonly used materials are basic plastics, ceramics, cement, glass and numerous metals such as titanium and aluminum. The demand for these materials will continue to increase, especially for titanium. Titanium is heavily used in the medical, aerospace, and automotive applications of 3D printing, in the form of personalised surgical implants and fuel tanks.
To sustain 3D printing’s use of titanium when it hits the mainstream, the global pipeline for the semi-precious metal should be secured for the following years. Thankfully, several mines in South America are already on their way to produce high-grade supply of titanium, such as White Mountain Titanium Corporation (OTCQB: WMTM) in Chile. White Mountain Titanium sits on a deposit in Cerro Blanco that contains 112 million tons of high-grade rutile. Companies applying 3D printing can benefit from it once the mine starts distributing the supply around the world.
To contact the writer, email: vittoriohernandez@yahoo.com