Spinal Fusion Surgery Makes Use Of First 3D-Printed Titanium Cervical Implant
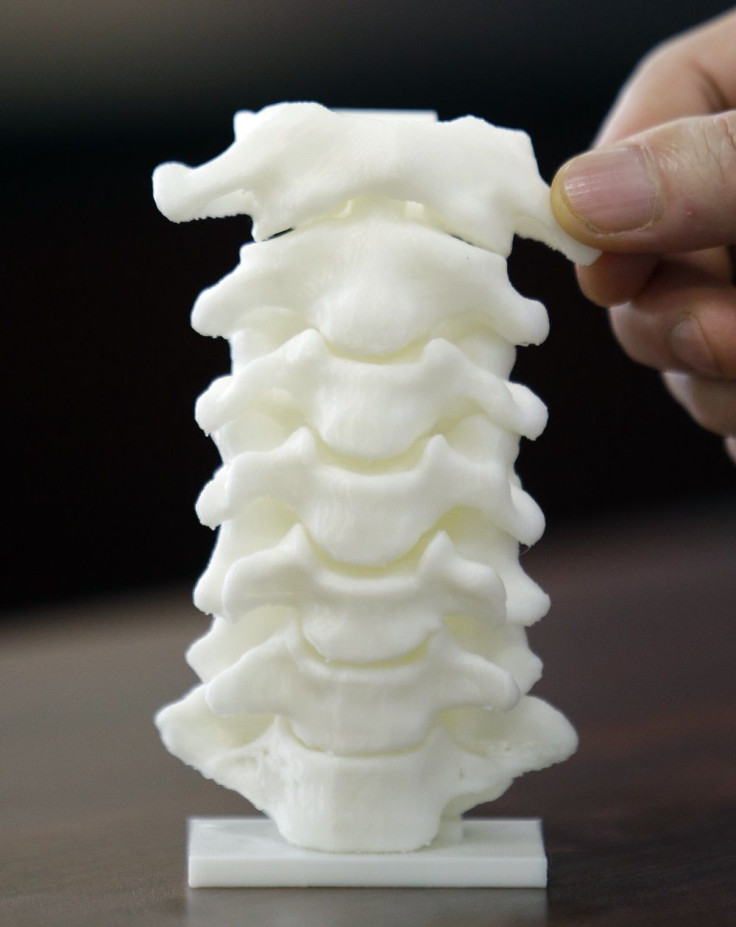
For the first time in history, a team of German surgeons has successfully performed a spinal fusion operation using a 3D-printed titanium cervical implant rather than the traditional bone grafts and metal hardware like plates and screws. The operation was planned and executed by UweSpetzger, professor and chairman of the Department of Neurosurgery of the Klinikum Karlsruhe in Germany, who believes that "the future of patient individualized spinal implants has begun." In a press release, Spetzger said, "We are fascinated by the possibilities of this new technology combining modern computer-aided design and custom-made manufacturing of a high-tech cervical implant."
The personalized cervical implant, which mimics the trabecular bone structure, was the result of a collaboration between 3D Systems and EIT Emerging Implant Technologies GmbH, a newly formed company dedicated to 3D-printed implant solutions. The company creates titanium implants with micro-, macro-, and nano-structural features that provide high stability and speeds up the bone healing and fusion process. These features also provide excellent bone-implant contact and negate the need for a bone graft.
Furthermore, the individualisation of the implant makes sure that it is an exact fit and perfect match to the patient's anatomy. Hence, the implant is less likely to shift around, destroy the structural integrity of the surrounding bones, or suffer delays in fusion common to standard implants.
"In two to three years, we will be able to provide individualized series implants at reasonable cost," said Stephanie Eisen, CEO of EIT. "Individualization will deliver better implants, faster and easier surgery, and better patient outcome."
Another goal of EIT is to reduce reoperation rates on people having spinal fusion surgeries. According to the University of Maryland Medical Center, traditional methods that use bone grafts and metal hardware are susceptible to complications, like hardware fracture and implant migration. Such things are frequent causes of spinal reoperation, as bone fusion does not occur. "The reoperation rates in spine surgery are by far higher than, for example, with hip or knee implants. It is our mission to change this," said Eisen.
But the 3D-printed titanium cervical implant is not the first 3D-printed implant that has been successfully used in surgery. In fact, the groundbreaking technology is swiftly gaining interest in the biomedical industry, thanks to success stories like the 3D-printed titanium bone that can replace segments lost to cancer, as well as the first titanium printed heel. A patient in Argentina also got a 3D-printed cranial implant after a stroke-related surgery and is now reported to be recovering and leading a normal life.
Despite the high prices of titanium in the market, the groundbreaking 3D-printing technology continues to pique the interests of the biomedical industry because of the promising innovations that it could bring to modern surgeries. In addition, there seems to be no shortage of titanium supply in the future, with new mines like that of Chilean-based miner White Mountain Titanium Corporation (OTCQB: WMTM) making positive developments towards their projects. Hence, there seems to be enough titanium metal to sustain the growing field of 3D-printed titanium implants.
To contact the writer, email: vittoriohernandez@yahoo.com