What Are the Core Advantages of Using a Solid Model in Product Design?
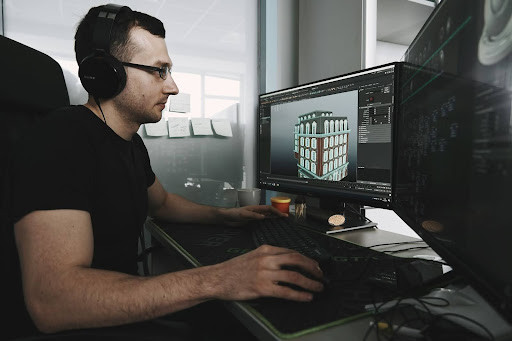
Technology in the fields of design and engineering is increasing at an exponential rate. One of the biggest advances in the field of product design is solid modelling. A solid model is a geometrically realistic 3D model created from a 2D draft. The draft contains information such as physical dimensions, materials to be used, how the components function together, and what the final object should look like once manufactured. 3D modelling software is then used to create a geometrically accurate representation of the design, which can be viewed from any angle or in sections. With that said, there are several core benefits to solid modelling.
1. Improved Designs
Solid modelling allows you to quickly generate accurate digital models of what the final product design should look like. This gives designers and engineers a better view of the overall design and allows them to identify any potential design errors or modification requirements before manufacturing. In addition, any design fixes or modifications can be done quickly in the program itself, rather than having to start from scratch. This, in turn, saves time and ensures the final completed product is an accurate representation of the design.
2. Saves Money
The process of designing prototypes can take up a lot of time and resources, which in turn leads to cost blowouts. Solid modelling takes much of the effort out of creating accurate 3D models and is capable of producing realistic 3D prototypes in a fraction of the usual time. All processes take place within the solid modelling program itself, which means no data needs to be converted and transmitted between software. In addition, creating accurate 3D representations of the final design cuts down the need for physical prototyping, which is a process that requires funding and resources for materials and production. Finally, solid modelling programs reduce the need to learn different systems, cutting down training and maintenance costs.
3. Faster Production
By decreasing the time needed to create realistic 3D prototypes of products, solid modelling also helps reduce the time needed to generate the final product. Much of the work can take place without the need to transfer data between other programs or teams since the solid modelling program handles a high percentage of the product creation process. Instead, all teams and stakeholders can access the program and make additions without having to wait for others. This leads to better collaboration and ensures there is no time wasted in getting the product to market.
4. Better Teamwork
Design, engineering, and manufacturing teams all need to be on the same page to ensure that they come up with the best quality products. When these teams are forced to work in isolation, the potential for creating quality products is greatly reduced. Solid modelling allows for greater collaboration between teams, each bringing their own knowledge and expertise to the task. In turn, increased collaboration allows teams to potentially come up with new strategies and manufacturing techniques, leading to better ways of creating products.
5. Higher Innovation
All manufacturers are looking for ways to improve their existing products or potentially create new products that can shake up the market. However, this can only be achieved when different teams are able to work together and share their knowledge and expertise. Solid modelling creates the space required for teams to collaborate and come up with the ideas needed to create innovative new designs. From testing new materials to changing the overall aesthetics, all teams can experiment with the 3D prototype to come up with new designs that can be tested and marketed, potentially leading to a new breakthrough in the industry.
© Copyright 2025 IBTimes AU. All rights reserved.